In this blog,
Picture this: You've just spent weeks perfecting a product design. The client loves it, but then drops a bombshell – they need it 20% smaller and in five different configurations. This might send you back to the drawing board in the traditional design world. But in the parametric universe? It's just a matter of tweaking a few parameters. We are here to take you to the future of design.
Parametric modeling isn't just a tool; it's a complete paradigm shift in how we approach design and engineering. At its core, parametric modeling is about creating designs driven by parameters – variables that control various aspects of your model. Change a parameter, and your entire design updates automatically, maintaining the relationships and rules you've defined.
But why should you care? The tasks that would take you days can now be done in hours or minutes. Explore design possibilities that you have never even thought of.
In this comprehensive guide, we dive deep into the parametric modeling revolution. Whether you're a seasoned pro looking to stay ahead of the curve or a curious newcomer ready to unlock new possibilities, get ready—you're in for an exciting ride through the modern design landscape. You'll discover how parametric modeling is transforming industries, from aerospace to architecture, and how it can give your business a competitive edge in an increasingly dynamic market.
What is Parametric Modeling?
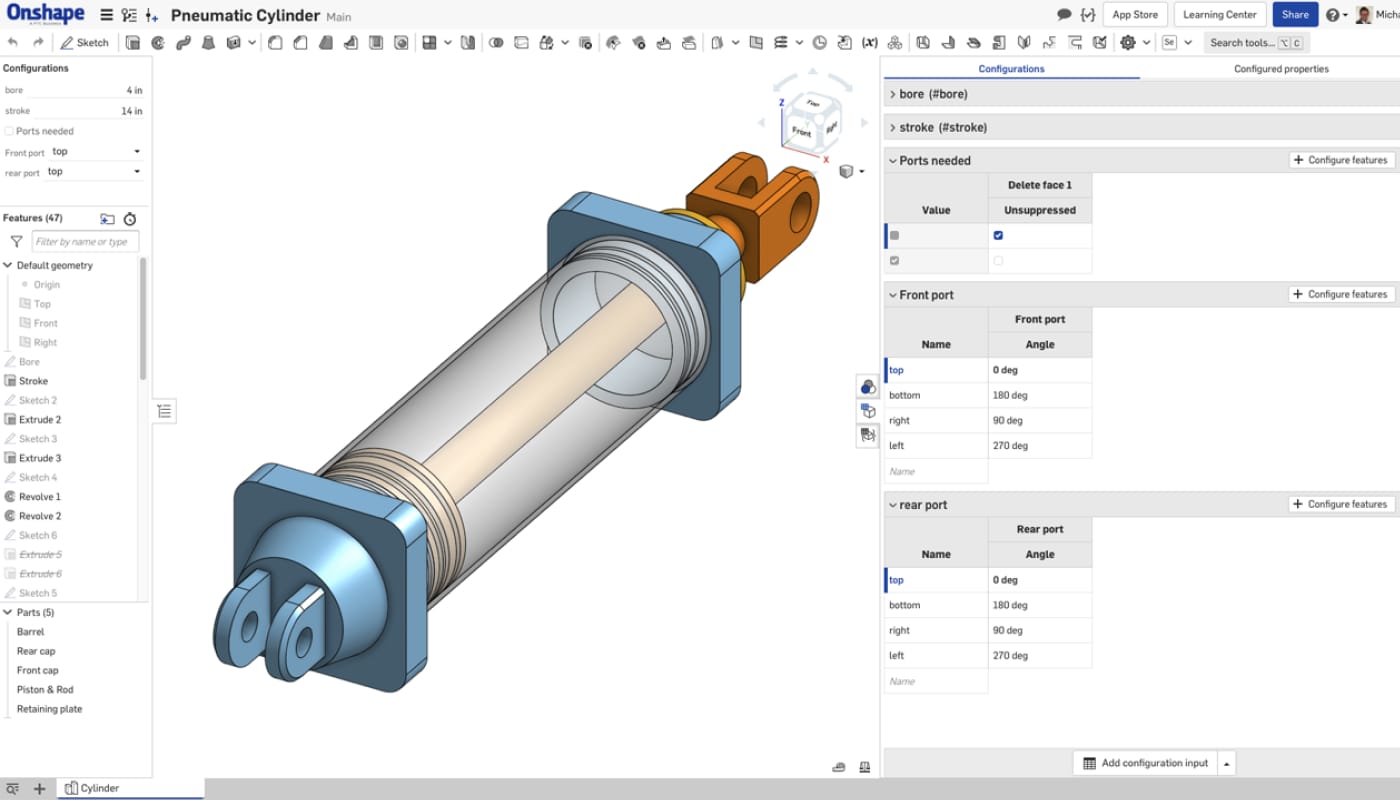
Parametric modeling is a method of creating models based on algorithms and parameters that define the relationships between different design elements.
These parameters are rules or constraints that dictate how various components of the model behave when changes are made. Instead of manually adjusting every part of a model, designers and engineers input values, and the model automatically updates itself to reflect those changes.
Imagine you're designing a chair. In traditional modeling, you’d have to manually alter each component (the legs, seat, backrest, etc.) if you wanted to change the height or dimensions. With parametric modeling, you define relationships between these components. For example, the height of the chair might be linked to the length of the legs. Change the leg length, and the entire chair adjusts accordingly.
Fundamentals of Parametric Modeling
To learn a technique or even being better at it, it is always essential to understand the basics of it. At its heart, parametric modeling is all about geometric relationships and rules. Unlike traditional CAD, where you draw static geometries, in parametric modeling, you create a set of instructions for how your design should behave.
Let’s take a quick look at the key concepts of parametric modeling:
- Parameters: These are the variables that drive your design. They can be dimensions, angles, material properties – anything you can assign a value to.
- Constraints: These define the relationships between different elements of your model. For example, you might constrain two lines always to be parallel.
- Features: These are the building blocks of your model, like extrusions, cuts, or fillets. In parametric modeling, features are linked to parameters and constraints.
- Dependencies: These are the magic sauce. Each element in your model knows how it relates to other elements, creating a web of interconnected parts.
Parametric vs. Polygonal Modeling: A Quick Comparison
To understand parametric modeling in a different light, it is better to compare it with traditional modeling.
Polygonal modeling is like sculpting with clay – you create geometry by pushing, pulling, and manipulating the surfaces directly. It's a flexible and intuitive way to model, but it can be time-consuming, especially if you need to make changes later on. Think of it like trying to reshape a clay sculpture after it's already dried – it's doable, but it's a lot of work.
On the other hand, parametric modeling is more like working with digital Lego blocks. Instead of sculpting surfaces, you define parameters and constraints that determine the geometry. This approach is great for making changes because you can simply adjust the parameters, and the model updates automatically. It's like being able to rebuild your Lego creation with a few clicks instead of having to disassemble and reassemble it manually.
For example, you are designing a table,
In the traditional approach, you draw the top and legs, specifying each dimension. Want to change the height? You'll have to redraw those legs.
Whereas with parametric modeling, when you define relationships – the legs are always touching the ground and the top. Set a "height" parameter. Now, change that single value, and your entire table adjusts automatically.
The power of parametric modeling lies in this ability to capture design intent. You're not just drawing shapes; you're encoding the logic of your design into the model itself.
The Parametric Modeling Process
Creating a parametric model is like writing a recipe for your design. Let's walk through the process:
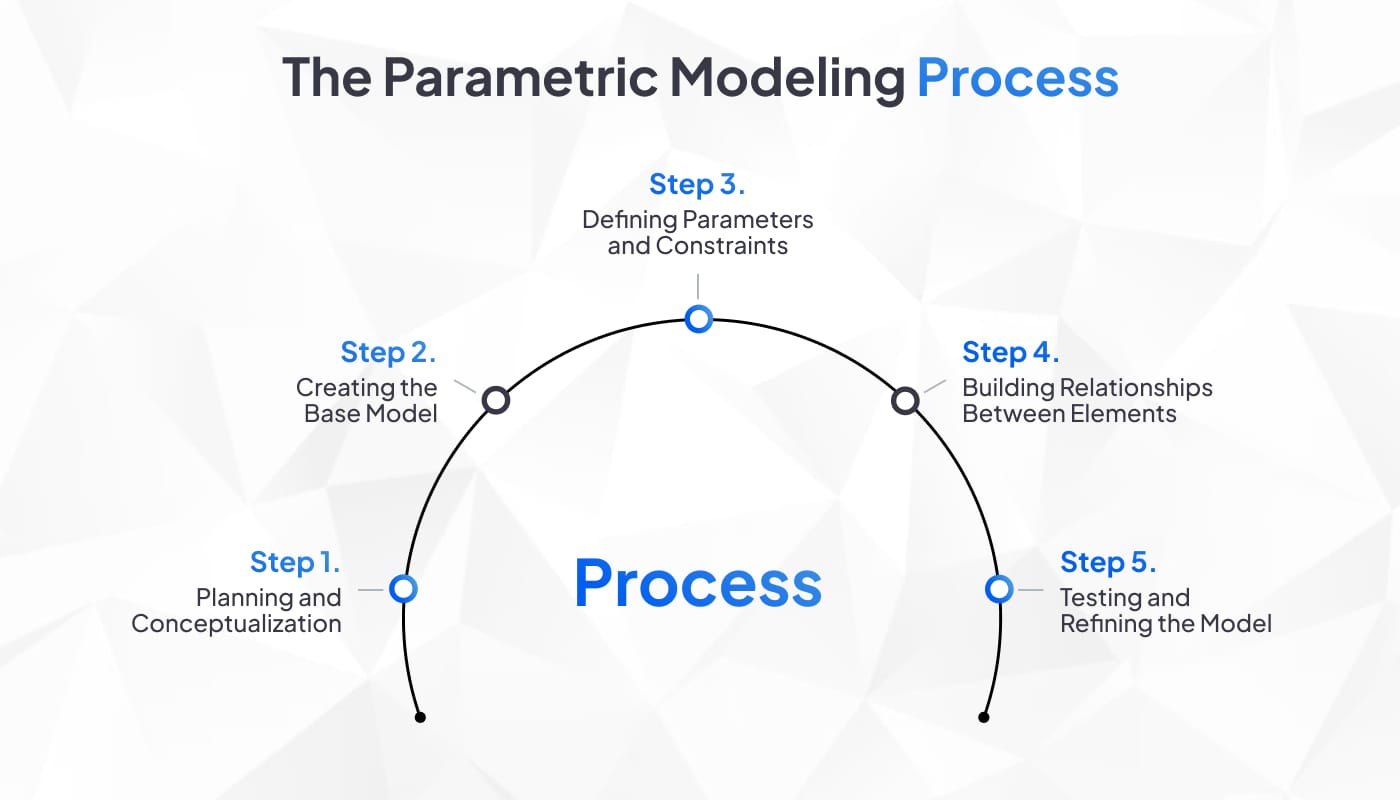
1. Planning and Conceptualization
Before you touch your software, start with good old-fashioned brainstorming so it becomes easier; think of questions like:
- What are the key features of your design?
- Which dimensions or properties might need to change?
- What relationships are crucial to maintain?
Pro Tip: Sketch out your ideas and label potential parameters. This roadmap will be invaluable as you build your model.
2. Creating the Base Model
Start with the core geometry of your design:
- Begin with 2D sketches, applying basic constraints (parallel, perpendicular, etc.).
- Create 3D features from these sketches.
- Keep it simple at first – you can add complexity later.
3. Defining Parameters and Constraints
Now, establish the variables and limitations that will guide the design process.
- Identify key dimensions and convert them to parameters.
- Name them clearly – future-you (or your colleagues) will thank you!
- Set up constraints that maintain critical relationships in your design.
4. Building Relationships Between Elements
Connect the elements in the model so they respond to changes in the parameters, creating a cohesive and dynamic design.
- Use equations to link parameters. Maybe the width is always twice the height?
- Create feature dependencies. For example, a hole might always be centered on a face, regardless of the face's size.
5. Testing and Refining the Model
Evaluate the model's performance and make adjustments as needed, ensuring it meets the design objectives and captures the intended logic.
- Change parameters and watch how your model reacts.
- Look for unexpected behaviors or failures.
- Refine your constraints and relationships as needed.
Remember, a good parametric model is like a well-oiled machine – all parts working together seamlessly as conditions change. It should always be easy to update the model, through this technique.
Tools and Software for Parametric Modeling
The right tool can make or break your parametric modeling experience. It is also essential to know which tool would be right for your needs. Let's explore some popular options; we’ll also mention their pros and cons so it gets easier for you! And also what are they best for!
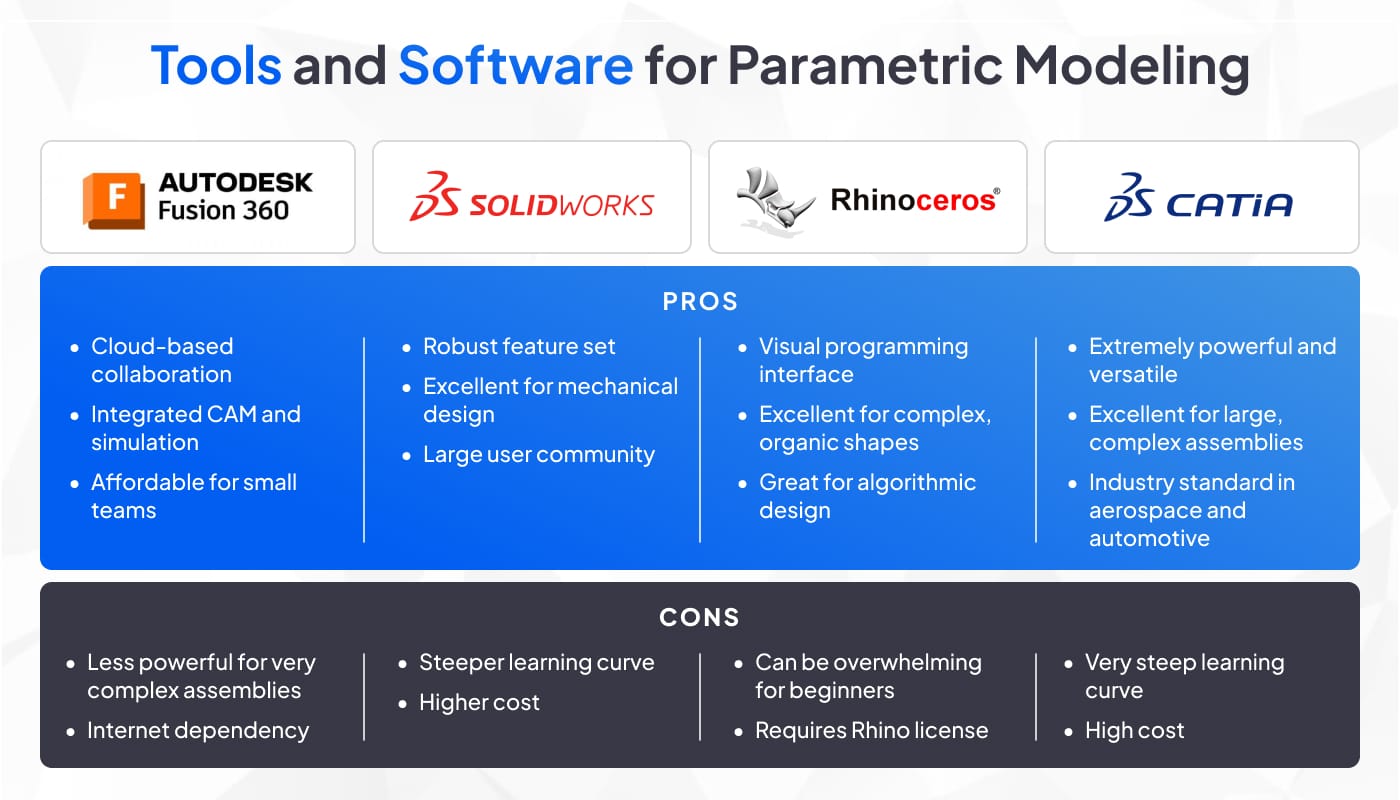
Autodesk Fusion 360
Fusion 360 is a cloud-based 3D CAD, CAM, and CAE tool that supports parametric modeling. It is particularly popular among product designers and engineers due to its comprehensive set of tools for design, simulation, and manufacturing.
Pros:
- Cloud-based collaboration
- Integrated CAM and simulation
- Affordable for small teams
Cons:
- Less powerful for very complex assemblies
- Internet dependency
Best For: Startups, small to medium businesses, product designers
SOLIDWORKS
SolidWorks is a popular choice in engineering and manufacturing. It provides a robust platform for creating parametric mechanical parts and assembly models. SolidWorks also offers powerful simulation tools, allowing engineers to test designs under real-world conditions before manufacturing.
Pros:
- Robust feature set
- Excellent for mechanical design
- Large user community
Cons:
- Steeper learning curve
- Higher cost
Best For: Mechanical engineers, larger manufacturing companies
Rhinoceros (Rhino)
Rhino is a versatile 3D modeling software often used in industrial design, architecture, and furniture design. One of its key features is Grasshopper, a visual programming tool that allows users to create parametric models by defining relationships between different components
Pros:
- Visual programming interface
- Excellent for complex, organic shapes
- Great for algorithmic design
Cons:
- Can be overwhelming for beginners
- Requires Rhino license
Best For: Architects, industrial designers, those working with complex geometries
CATIA
CATIA is a versatile and powerful parametric modeling tool widely used in industries like aerospace, automotive, and industrial design. Known for its advanced capabilities in creating complex 3D models and assemblies, CATIA excels in surface modeling, allowing designers to create intricate shapes with high precision.
Pros:
- Extremely powerful and versatile
- Excellent for large, complex assemblies
- Industry standard in aerospace and automotive
Cons:
- Very steep learning curve
- High cost
Best For: Large enterprises, aerospace, automotive industries
Choosing the Right Tool
When the time comes to choose the right tool, you have to be sure of what your needs are. We compiled a list of things to keep in mind when choosing the right tool for your project.
- Your Industry: Some tools are more common in certain fields.
- Learning Curve: How much time can you invest in training?
- Budget: Prices range from free to tens of thousands of dollars.
- Collaboration Needs: Will you be working in teams?
- Integration: How well does it fit with your existing tools?
Remember, the best tool is the one that fits your specific needs and workflow. Don't be afraid to try demos and talk to other users before making a decision.
Advanced Parametric Modeling Techniques
Ready to take your parametric modeling to the next level? Let's explore some advanced techniques that can supercharge your designs:
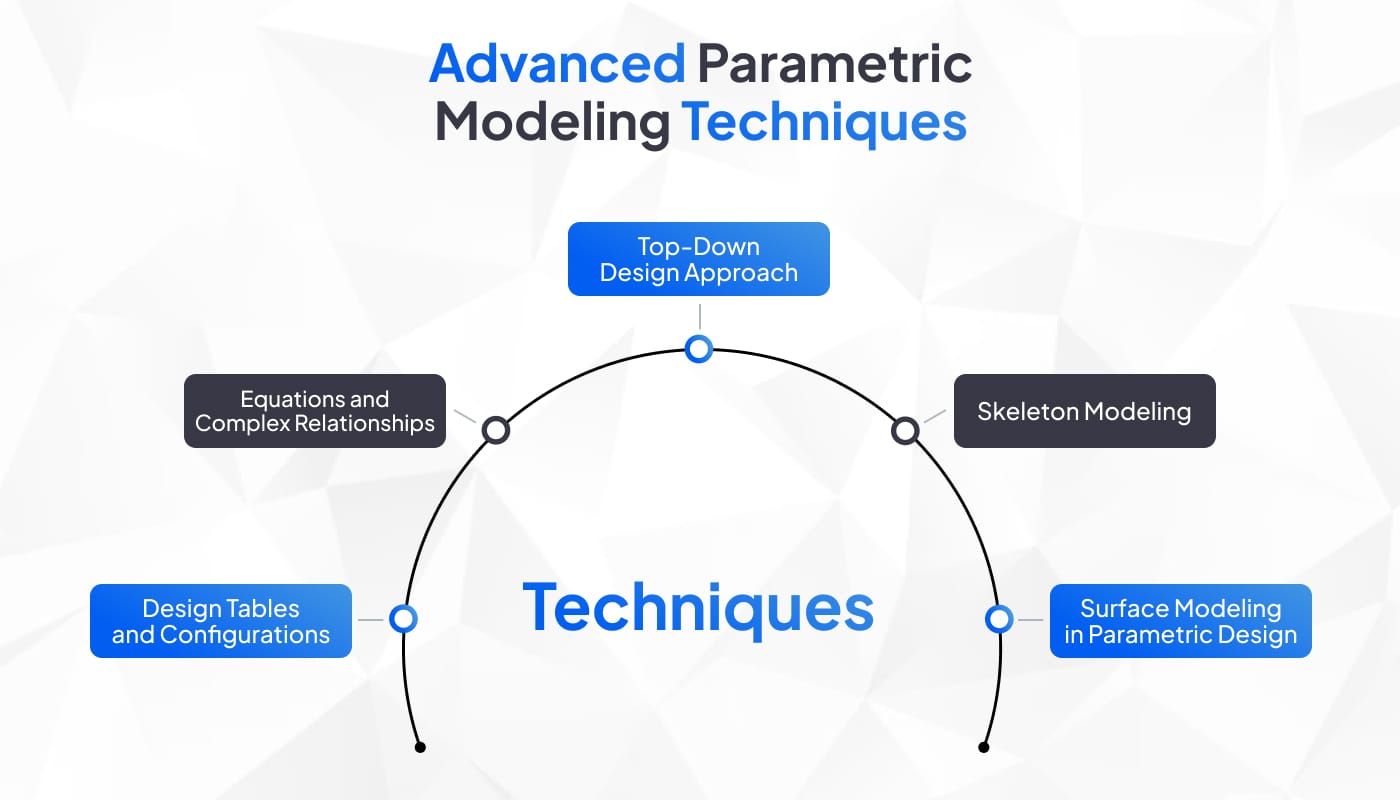
Design Tables and Configurations
Imagine creating multiple versions of a product with a single model. That's the power of design tables:
- Create a spreadsheet linking parameters to different configurations.
- Generate entire product families from one base model.
- Easily manage variations for different markets or use cases.
Example: A furniture company uses design tables to create 50 variations of a chair from a single parametric model, each optimized for different body types and styles.
Equations and Complex Relationships
Move beyond simple parameters to create sophisticated, interconnected designs:
- Use mathematical equations to define relationships between parameters.
- Implement if-then logic to create adaptive designs.
- Leverage trigonometry for angle-dependent features.
Real-world application: An aerospace engineer uses complex equations to ensure that as a wing's length changes, its cross-section adapts to maintain optimal lift characteristics.
Top-Down Design Approach
Start with the big picture and work your way down to the details:
- Create a master sketch or skeleton that drives your entire assembly.
- Ensure changes at the top level propagate through all components.
- Maintain design intent across complex assemblies.
This approach shines in products where the overall form is crucial, like in automotive design.
Skeleton Modeling
Create a simplified framework that drives your entire design:
- Build a basic structure of planes, axes, and key points.
- Use this skeleton to control multiple parts in an assembly.
- Easily modify overall proportions while maintaining relationships between components.
Skeleton modeling is particularly useful in machinery design, where the relationship between key components is critical.
Surface Modeling in Parametric Design
Combine the power of surface modeling with parametric control:
- Create complex, organic shapes with precise control.
- Use parameters to control surface curvature and continuity.
- Blend surfacing techniques with solid modeling for ultimate flexibility.
This technique is a game-changer in industrial design, allowing for the creation of aesthetically pleasing, yet highly engineered products.
Applications of Parametric Modeling
Parametric modeling isn't just a niche tool – it's revolutionizing design across various industries with various key features that are unique to it. Let's explore how different sectors are leveraging this powerful approach:
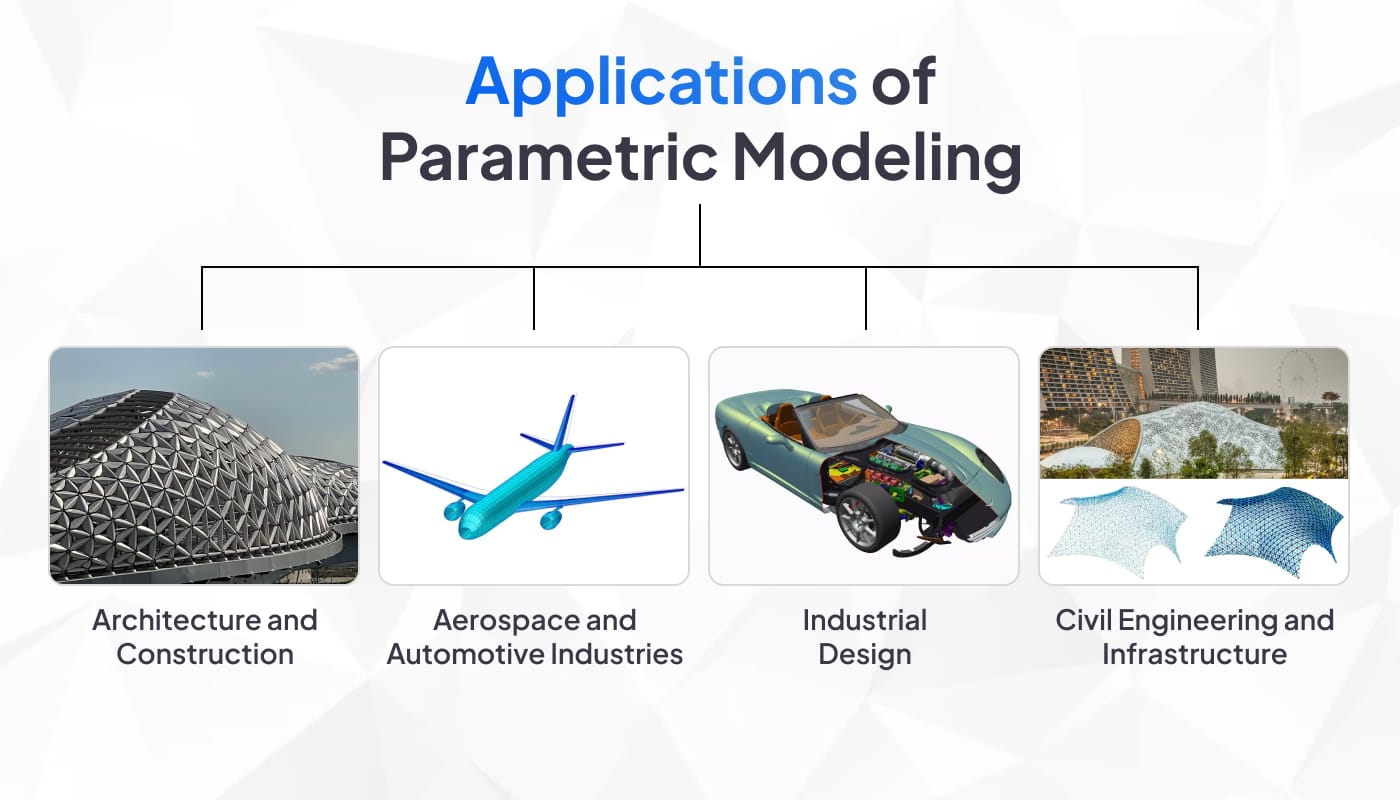
Architecture and Construction
In architecture, parametric modeling allows for the creation of complex, organic forms that would be difficult or impossible to design using traditional methods. It enables architects to explore more creative designs while ensuring that structures remain functional and accessible. In addition, it lets you rapidly iterate designs based on client feedback and any constraints found on the construction site.
For instance, parametric tools have been used to design iconic buildings such as the Gherkin in London, where the complex geometric form is driven by parameters controlling the building’s structure and façade.
Aerospace and Automotive Industries
Parametric modeling is widely used in the aerospace and automotive industries, where precision and performance are crucial. It helps design complex aerodynamic surfaces that adapt to different flight conditions.
In automotive industries, it optimizes the vehicle’s structure for weight reduction without compromising safety. One of the key benefits of this industry is that parametric modeling allows the creation of modular designs that can be easily customized for different models.
Airbus used parametric and generative design techniques to create bionic partition walls for the A320, resulting in structures that are 45% lighter than traditional designs.
Industrial Design
In industrial design, parametric modeling allows for rapid prototyping and testing of products. By adjusting parameters, designers can create different iterations of a product to optimize for performance, materials, and aesthetics. This is particularly valuable in sectors like consumer electronics, where rapid product development cycles are essential for staying competitive.
It helps develop customizable designs for mass personalization while optimizing product aesthetics and ensuring manufacturability.
Civil Engineering and Infrastructure
Engineers use parametric modeling to design and optimize complex systems. Civil engineering also uses parametric models to design bridges, tunnels, and other infrastructure projects. Engineers can quickly test different design options by defining parameters such as load-bearing capacity or material properties and find the best solution.
The Millau Viaduct in France, one of the tallest bridges in the world, used parametric modeling to optimize its design for both aesthetics and structural performance.
Benefits of Parametric Modeling for Businesses: The Competitive Edge
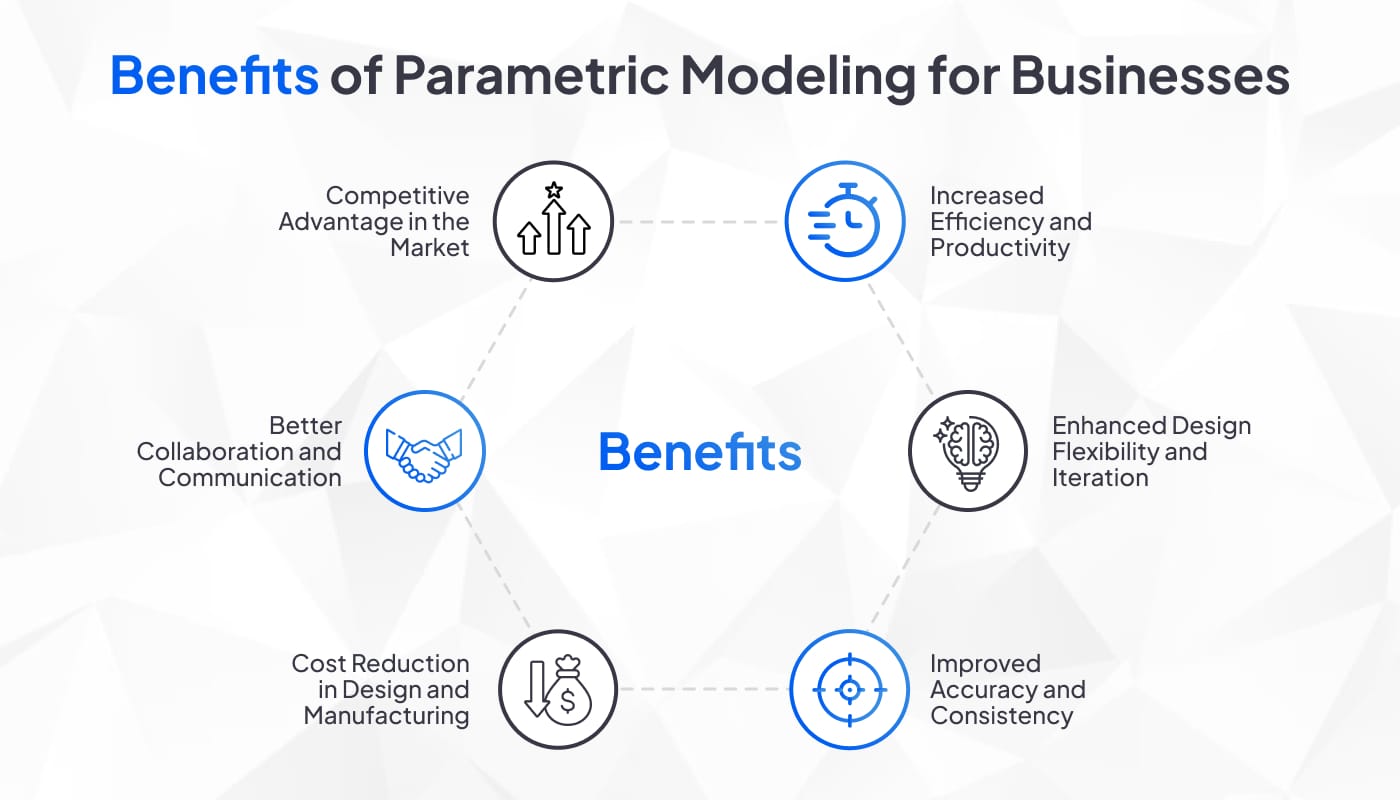
Adopting parametric modeling isn't just about keeping up with technology – it's about gaining a significant competitive advantage. Let's break down the business benefits:
Increased Efficiency and Productivity
Time is money, and parametric modeling is a time-saving powerhouse:
- Reduce design iteration time by up to 80% compared to traditional methods.
- Automate repetitive tasks, freeing up designers for creative problem-solving.
- Quickly generate multiple design options to present to clients.
ROI Example: A consumer electronics company reduced their product development cycle from 18 months to 6 months after implementing parametric modeling, allowing them to beat competitors to market.
Enhanced Design Flexibility and Iteration
In a world where change is constant, flexibility is key:
- Easily adapt designs to changing requirements without starting from scratch.
- Explore a wider range of design possibilities in less time.
- Quickly create product variations for different markets or user groups.
Case in Point: A furniture manufacturer uses parametric models to offer customers millions of possible configurations, all generated from a handful of base designs.
Improved Accuracy and Consistency
Reduce errors and maintain quality across your product line:
- Ensure design intent is maintained even as changes are made.
- Reduce manufacturing errors by automating the creation of production documentation.
- Maintain consistency across product families and versions.
Quality Impact: An aerospace supplier reduced part rejection rates by 35% after implementing parametric modeling, thanks to improved design consistency and automated checks.
Cost Reduction in Design and Manufacturing
Parametric modeling can significantly impact your bottom line:
- Reduce physical prototyping needs through accurate digital models.
- Optimize designs for material usage and manufacturing processes.
- Minimize costly late-stage design changes.
Savings Spotlight: A automotive parts manufacturer saved $2 million annually in material costs by using parametric modeling to optimize part designs for minimal material usage while maintaining performance standards.
Better Collaboration and Communication
Enhance teamwork and client relationships:
- Easily share and modify designs across teams and departments.
- Improve communication with clients by quickly visualizing design changes.
- Streamline collaboration between design and manufacturing teams.
Collaboration Win: An architectural firm increased client satisfaction scores by 40% after implementing parametric modeling, thanks to their ability to quickly visualize and modify designs during client meetings.
Competitive Advantage in the Market
Stay ahead of the curve and differentiate your business:
- Offer more innovative and customizable products.
- Respond faster to market trends and customer demands.
- Take on more complex projects with confidence.
Market Leader: A sportswear company leveraged parametric modeling to launch a line of custom-fit shoes, capturing a niche market and increasing their market share by 15% in the first year.
By embracing parametric modeling, businesses can not only streamline their design and production processes but also open up new possibilities for innovation and customer satisfaction. In an increasingly competitive global market, the adaptability, efficiency, and creative potential offered by parametric modeling can be the difference between leading the pack and falling behind.
Challenges and Limitations of Parametric Modeling
While parametric modeling offers tremendous advantages, it’s not without its challenges. Let’s explore some of the most common roadblocks businesses encounter when implementing parametric modeling.
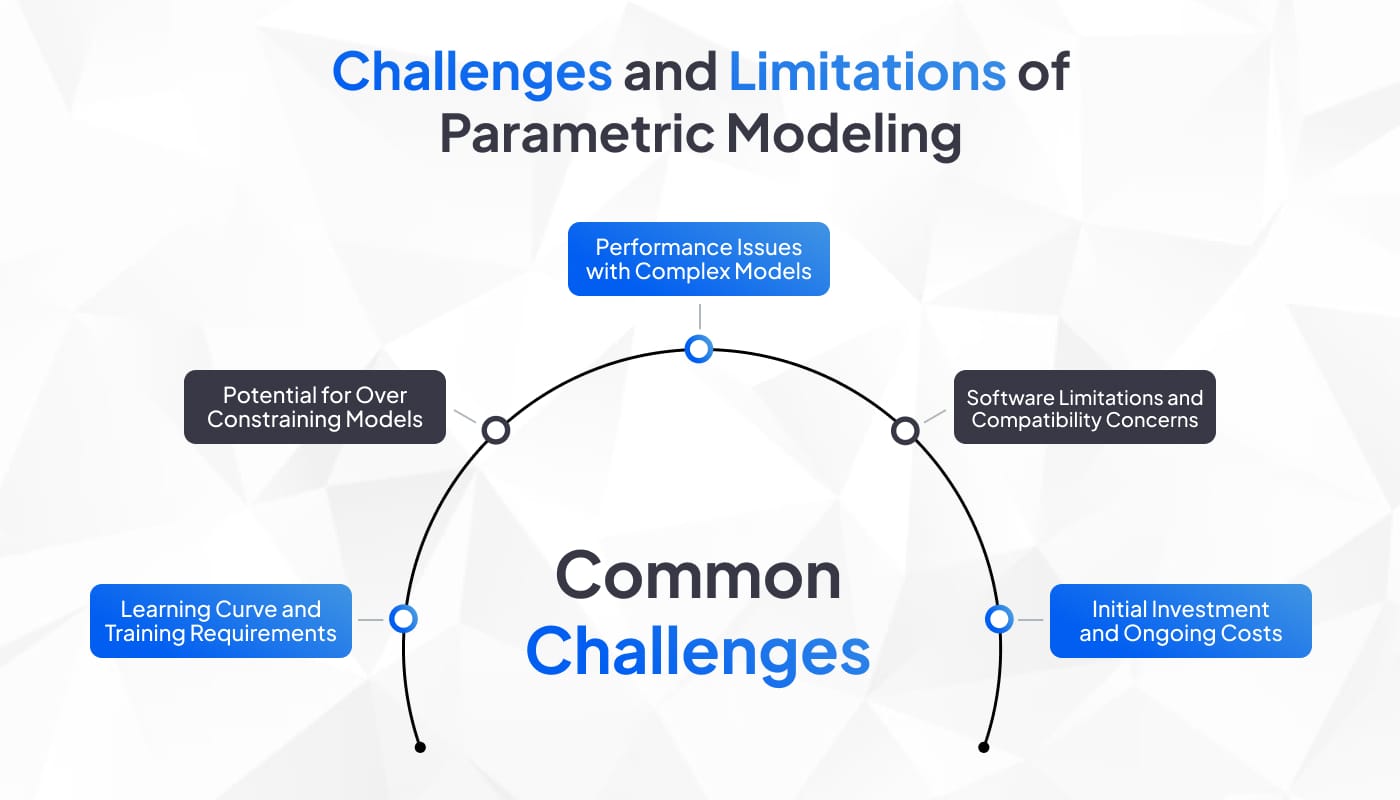
Learning Curve and Training Requirements
Getting your team up to speed on parametric modeling can be a hurdle:
- Steep Learning Curve: Parametric modeling demands a deep understanding of both the software and the underlying design principles. This isn’t a tool you can pick up overnight.
- Specialized Training: Unlike traditional CAD systems, parametric modeling requires specific skills, especially in constraint-based design and managing relationships between parameters.
- Time and Resources: Training teams can take weeks, even months, depending on their familiarity with CAD tools. Investing in ongoing training is essential to stay updated with software advancements.
Training Cost Example: A mid-sized manufacturing firm spent over $50,000 on training and implementation for parametric modeling tools. However, they recouped the cost within the first year through increased design efficiency.
Potential for Over-Constraining Models
Parametric modeling thrives on constraints, but too many can backfire:
- Over-Constraining: Adding too many relationships and dependencies between elements can make a model rigid. Changes in one part of the model can cascade into unintended consequences.
- Model Complexity: Over-constraining also makes it harder to troubleshoot or refine models, as even minor adjustments can lead to a breakdown in the design logic.
Real-World Issue: A product development firm experienced project delays when a highly constrained model collapsed during a late-stage design revision, requiring extensive rework.
Performance Issues with Complex Models
As parametric models grow in complexity, so do the demands on system performance:
- Computational Overload: Large or intricate models can slow down processing speeds, causing lag during editing and testing.
- Resource-Heavy Software: Running advanced parametric modeling software requires powerful hardware, which can mean additional investment in IT infrastructure.
Performance Strain Example: An architecture firm found that their complex building models caused frequent system crashes, leading to increased project timelines due to the need for model simplification.
Software Limitations and Compatibility Concerns
No tool is perfect, and parametric modeling software can have its own constraints:
- Software-Specific Limitations: Each parametric modeling platform has its own set of strengths and weaknesses, making it vital to choose the right tool for the job.
- Compatibility Issues: Sharing parametric models across teams or departments using different software can lead to compatibility issues, especially when exchanging files between different CAD systems.
Compatibility Challenge: A multinational engineering firm faced collaboration difficulties when one department used a different parametric software, causing issues when integrating design files.
Initial Investment and Ongoing Costs
Adopting parametric modeling comes with a price tag:
- Software Costs: Parametric modeling tools often come with subscription fees or licensing costs, which can be substantial depending on the scale of usage.
- Hardware Upgrades: High-end hardware is necessary to fully leverage parametric modeling software, leading to additional costs.
- Maintenance and Support: Ongoing software updates, troubleshooting, and maintaining licenses also add to the overall expense.
Investment Breakdown: A small design firm estimated their initial investment in parametric modeling software and hardware upgrades at $75,000, but saved $250,000 in design and manufacturing costs over three years.
Despite these challenges, the long-term benefits of parametric modeling often outweigh the upfront costs and hurdles. A well-prepared approach, complete with adequate training and support, can help mitigate these challenges and unlock the full potential of parametric design.
Best Practices in Parametric Modeling
To fully harness the power of parametric modeling, adopting best practices is crucial. Here are the key steps to ensure your team works efficiently and effectively.
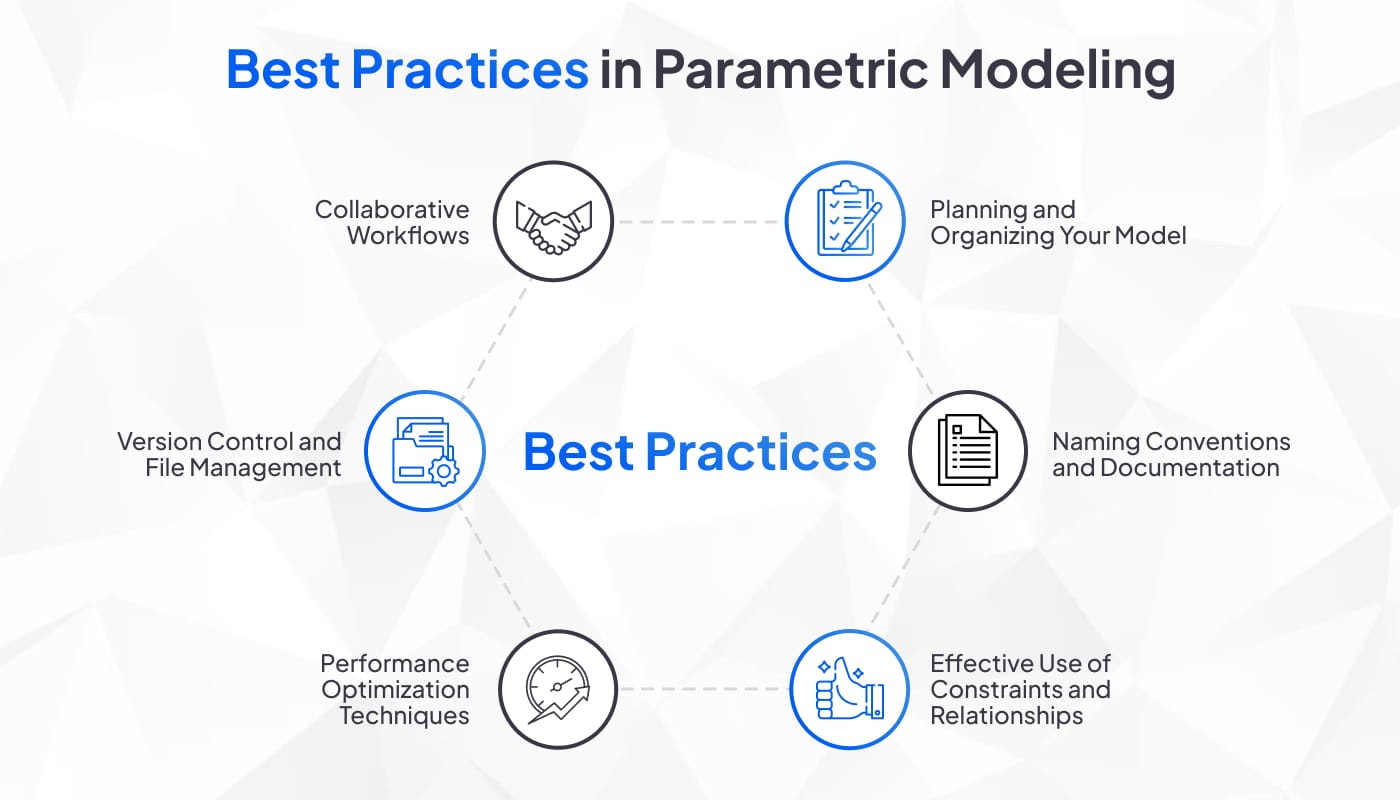
Planning and Organizing Your Model
A well-organized model lays the foundation for successful parametric design:
- Start with a Plan: Before jumping into the design, clearly define the parameters, relationships, and constraints. Map out the hierarchy of elements, ensuring each one connects logically.
- Keep It Simple: Avoid unnecessary complexity in your model. Use only the parameters you need to maintain flexibility without overcomplicating relationships.
- Design with the End in Mind: Consider how the model will evolve during the design process and future changes. Ensuring scalability in your initial plan saves time later.
Pro Tip: Start with a rough sketch or flowchart that outlines how different components will interact within the model before diving into software.
Naming Conventions and Documentation
Proper documentation and naming conventions are key to maintaining an organized workflow:
- Consistent Naming: Establish a standardized system for naming elements and parameters. Clear and consistent names make it easier for the team to understand the model’s structure.
- Documentation: As models grow in complexity, document critical steps, decisions, and changes. This helps ensure that team members or external collaborators can quickly get up to speed.
Example: A civil engineering firm used standardized naming conventions across all projects, reducing onboarding time for new team members by 25%.
Effective Use of Constraints and Relationships
Constraints are at the core of parametric modeling, but effective use is essential:
- Avoid Over-Constraining: As mentioned earlier, over-constraining can lead to rigid models. Balance flexibility with stability by carefully choosing which elements need constraints.
- Prioritize Key Relationships: Focus on the most critical relationships that impact the design intent. By creating a clear hierarchy of dependencies, you can manage changes more effectively.
Pro Tip: Use driving dimensions (parameters that control other dimensions) sparingly. Too many driving dimensions can make troubleshooting difficult.
Performance Optimization Techniques
As your models grow in complexity, optimizing performance becomes a priority:
- Modularize Your Design: Break large models into smaller, manageable modules. This not only improves system performance but also allows for easier modifications.
- Limit Parametric Depth: Keep the number of dependencies manageable. Reducing excessive layers of parametric depth helps avoid performance slowdowns and minimizes the risk of design errors.
Optimization in Action: A furniture design firm reduced system lag by 30% by compartmentalizing large assemblies into smaller, easily managed subcomponents.
Version Control and File Management
Efficient file management can save hours of rework and frustration:
- Version Control Systems: Implement a version control system (VCS) to track model changes and revisions. This ensures that no work is lost and allows teams to revert to previous versions if needed.
- File Organization: Organize files into a logical folder structure, categorizing by project, version, and design phase. Keep the most up-to-date versions easily accessible.
VCS Success: A product design company reduced design rollback errors by 40% after adopting a VCS to manage their parametric models across different teams.
Collaborative Workflows
Collaboration is key in parametric modeling, especially in complex projects involving multiple teams:
- Shared Models: Use cloud-based tools or a shared server to allow multiple team members to access and modify models in real-time.
- Regular Reviews: Establish a regular review process where stakeholders can provide feedback on parametric models. This helps identify issues early and ensures alignment across teams.
Collaboration Win: An automotive design team cut their design cycle by 25% by integrating collaborative parametric modeling workflows, allowing for simultaneous edits and reviews.
Case Studies
Parametric modeling has revolutionized design processes across various industries. In this section, we will talk about some fantastic examples that were led by parametric modeling, what challenges they faced, and their solutions.
Let's explore some real-world examples that showcase its power and impact.
The Beijing National Stadium ("Bird's Nest")
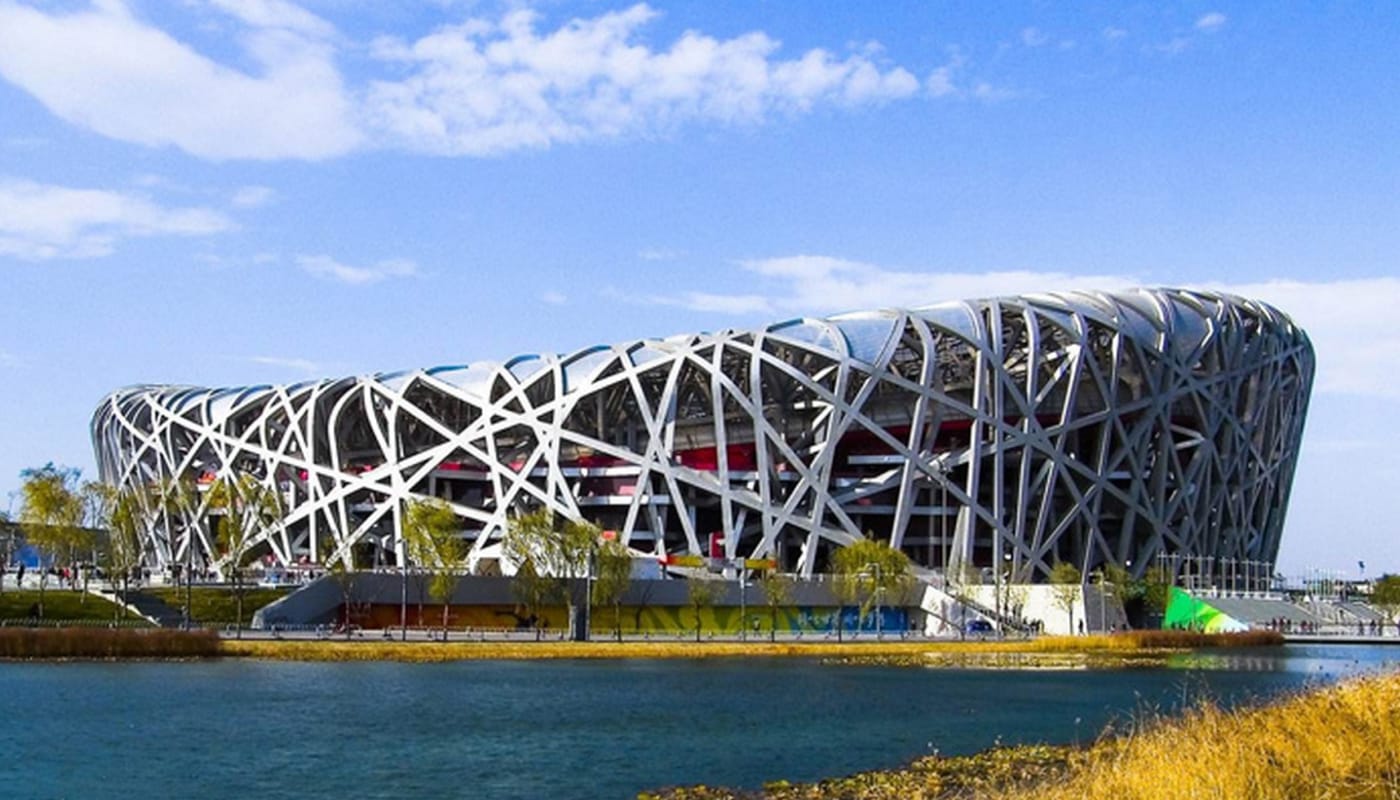
The iconic Beijing National Stadium, built for the 2008 Olympics, is a testament to the power of parametric modeling in architecture. The Bird’s Nest designed by Herzog & de Meuron, this complex structure was made possible through advanced parametric design techniques.
Challenge: Create a visually striking yet structurally sound stadium with an intricate, interwoven appearance.
Solution: Using parametric modeling, the architects were able to:
- Generate and iterate on complex geometric patterns
- Optimize the structure for both aesthetics and stability
- Efficiently manage the placement of thousands of steel beams
Outcome: The resulting design not only became an architectural landmark but also demonstrated significant material efficiency, reducing steel usage by 20-30% compared to traditional design methods.
Boeing 787 Dreamliner
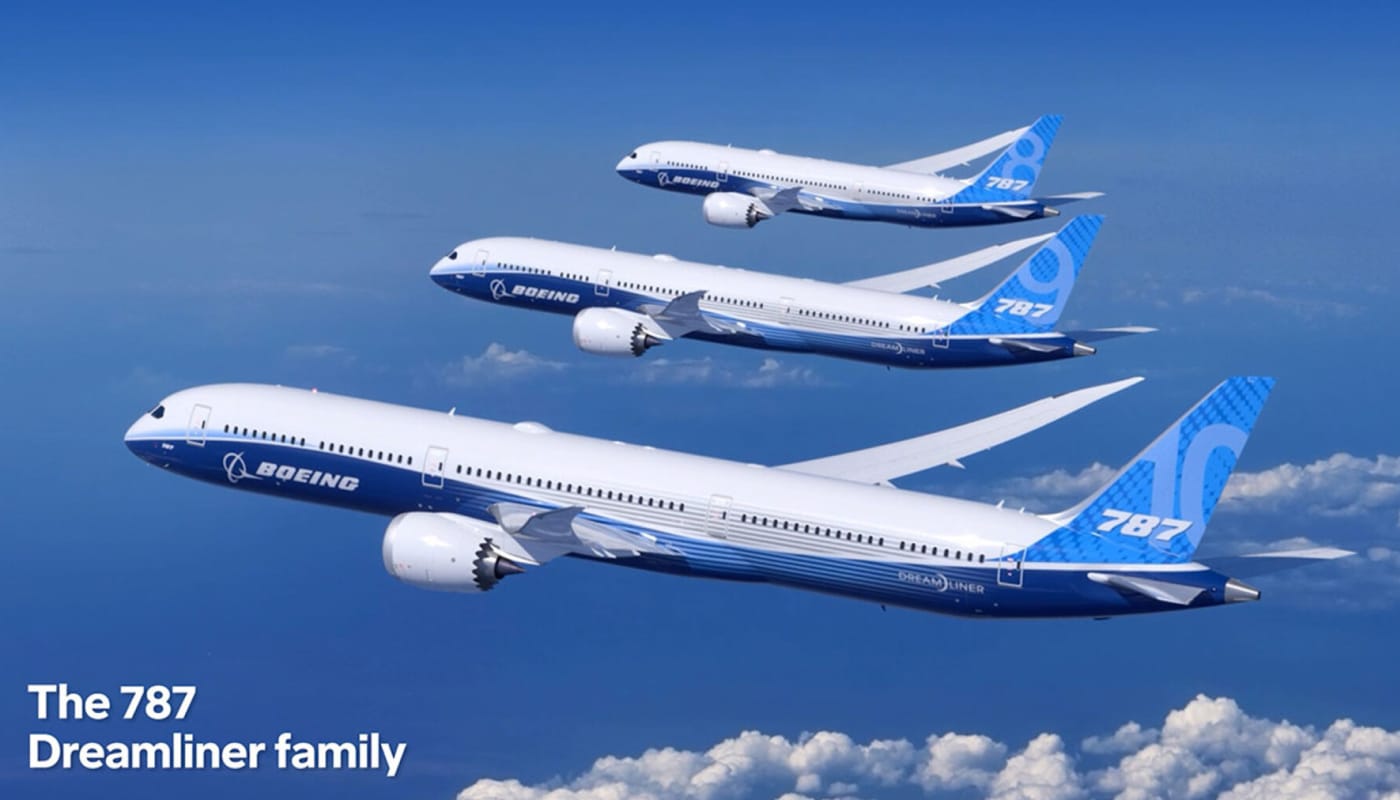
Boeing's 787 Dreamliner represents a leap forward in aircraft design, largely thanks to parametric modeling.
Challenge: Design a more fuel-efficient, comfortable, and environmentally friendly aircraft.
Solution: Boeing employed parametric modeling to:
- Optimize the aircraft's aerodynamics
- Design a more efficient wing shape
- Integrate complex systems within a streamlined fuselage
Outcome: The 787 Dreamliner achieved 20% better fuel efficiency than its predecessors, set new standards for passenger comfort, and revolutionized the aviation industry.
Parametric modeling offers several key benefits for design and engineering. It allows for the creation of complex, innovative designs that traditional methods can't quickly achieve. The quick iteration and optimization capabilities lead to significant improvements in how designs perform and how efficient they are.
This modeling approach also helps different experts like architects and engineers work together more effectively, resulting in better-integrated projects. While getting started with parametric modeling can be costly regarding tools and training, the payoff is often substantial when it comes to producing higher quality, more efficient, and more innovative designs.
Emerging Trends in Parametric Modeling
The field of parametric modeling is continuously evolving. Here are some exciting trends shaping its future:
Integration with Artificial Intelligence and Machine Learning
AI and ML are being incorporated into parametric modeling tools, offering capabilities like:
- Automated design optimization
- Predictive modeling based on historical data
- Intelligent suggestion of design alternatives
For example, Autodesk's Generative Design tool uses AI to explore thousands of design options based on specified constraints and goals.
Cloud-Based Parametric Modeling Platforms
Cloud platforms are transforming how designers collaborate and access computational resources:
- Real-time collaboration on complex models
- Access to powerful computing resources for intensive simulations
- Version control and easy sharing of models across teams
Onshape, a fully cloud-based CAD system, exemplifies this trend, allowing teams to work on the same model simultaneously from anywhere in the world.
Generative Design and Topology Optimization
These advanced techniques are pushing the boundaries of what's possible in design:
- Generative design uses algorithms to explore multiple design solutions based on set parameters and goals.
- Topology optimization refines designs for maximum performance with minimum material use.
Companies like Airbus are using these techniques to create lighter, stronger aircraft components, significantly reducing weight and fuel consumption.
Getting Started with Parametric Modeling
When you start something new, it is always good to have a guide to check off the tasks you have completed and what is left. So, we have made an easy-to-follow guide on how to start with Parametric Modeling. We’ll keep the points brief, so it’s a quick read.
Assessing Your Needs and Goals
Before choosing a tool or starting a project, consider:
- What types of designs will you be creating?
- What level of complexity do you need?
- How will parametric modeling integrate with your existing workflows?
Choosing the Right Software
Popular parametric modeling software includes:
- Autodesk Fusion 360: Great for product design and manufacturing
- SolidWorks: Widely used in mechanical engineering
- Grasshopper (Rhinoceros 3D plugin): Popular in architecture and industrial design
- CATIA: Favored in aerospace and automotive industries
Consider factors like industry-specific features, learning curve, and cost when making your choice.
Training and Skill Development Strategies
To build your parametric modeling skills:
- Start with tutorials provided by your chosen software vendor
- Take online courses on platforms like Coursera or Udemy
- Join user communities and forums to learn from peers
- Practice regularly with small, manageable projects
- Attend workshops or webinars for advanced techniques
Building Your First Parametric Model: A Step-by-Step Guide
- Start with a simple object (e.g., an adjustable bracket)
- Sketch the basic shape
- Add dimensions and constraints
- Create parameters for critical dimensions
- Build relationships between parameters
- Test the model by modifying the parameters
- Refine and optimize as needed
The Future of Parametric Modeling
As technology rapidly evolves, so will the world of Parametric Modeling. When we look ahead, several trends are likely to shape the future of parametric modeling
Predictions for Technological Advancements
- AI-Driven Design Assistants: Future parametric modeling tools may include AI assistants that can suggest design improvements, predict potential issues, and even generate entire design concepts based on specified requirements and deploy predictive modeling to the user's needs. Some additional use cases that come to mind are the automation of repetitive tasks, which take up a lot of time in the whole pipeline.
- Quantum Computing Integration: As quantum computing matures, it could dramatically enhance the processing power available for complex parametric models, enabling real-time optimization of incredibly complex systems.
- Advanced Materials Simulation: Parametric models may soon incorporate sophisticated materials science simulations, allowing designers to fine-tune material properties alongside geometric parameters.
Potential Impacts on Various Industries
- Architecture: We may see entire cities designed parametrically, optimizing for factors like energy efficiency, traffic flow, and quality of life.
- Healthcare: Parametric modeling could revolutionize the design of prosthetics and implants, creating perfectly customized solutions for each patient.
- Aerospace: Future aircraft and spacecraft designs may be fully optimized through parametric and generative design, pushing the boundaries of efficiency and performance.
- Fashion: Parametric design tools could enable mass customization of clothing, allowing consumers to tweak designs to their exact preferences and measurements.
To remain competitive in the rapidly changing world of design and engineering, professionals should adopt a few key strategies. It's crucial to embrace ongoing learning and stay up-to-date with new technologies and their possible uses.
Trying out fresh tools and methods as they emerge is important, as is working with experts from different fields to spark innovation. Additionally, it's worth exploring how parametric modeling might be applied in unique ways within your specific industry. By following these approaches, designers and engineers can better prepare themselves for future challenges and opportunities in their field.
Parametric Modeling for the Win?
Parametric modeling is transforming design and engineering, enabling the creation of complex, adaptive designs that were previously impractical. While mastering parametric modeling takes time, the payoff in terms of design quality and innovation is substantial.
As technologies like AI and VR advance, parametric modeling is set to become even more powerful and user-friendly. In an increasingly complex world with rapidly changing needs, this approach is becoming essential for competitive design and engineering.
The takeaway is clear: embracing parametric modeling now, by investing in tools and developing skills, is crucial for success in this new era.
In conclusion, parametric modeling is revolutionizing the fields of design and engineering. Its ability to create complex, optimized designs while increasing efficiency makes it an indispensable tool for modern professionals.
As technology continues to evolve, parametric modeling will only grow more powerful and accessible. For those in design and engineering, embracing this paradigm shift is not just an opportunity, but a necessity to remain competitive and innovative in the years to come. The future of design is parametric, and those who adapt early will be best positioned to leverage its vast potential.